Changeover in production so fast it’s redefining industry standards for small and medium volumes.
Benefit from four decades of industry experience and a commitment to quality with the Universal range from Tommy Nielsen. It’s the ideal solution for reliable and flexible packing of medical devices and pharmaceutical products. Featuring a height-adjustable function, the Universal range ensures an ergonomically optimal working height, promoting efficiency and comfort during operation. In addition, the range is compatible with clean room environments, meeting stringent hygiene standards.
With customizable features and a straightforward interface, it's designed to optimize your operations and meet the highest industry standards, ensuring great performance and peace of mind.
Want to know more about our Universal range and how it can optimize your medical packaging process?
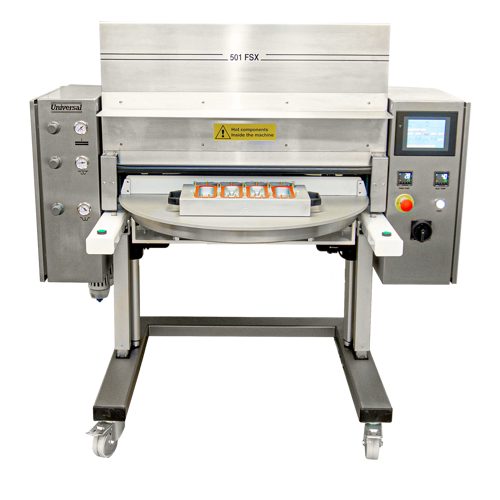
Efficiency in Action:
Form, fill, and seal in one cycle.
Experience the efficiency of forming, filling, and sealing your packaging in a single operation with Universal. Its semi-automatic design allows for smooth integration into your workflow, offering the flexibility to reprogram for either forming or sealing as needed. Simply load precut sheets or pre-punched blanks of blister material and lid, and let the machine do the rest.
Dimensions by machine model (in mm)

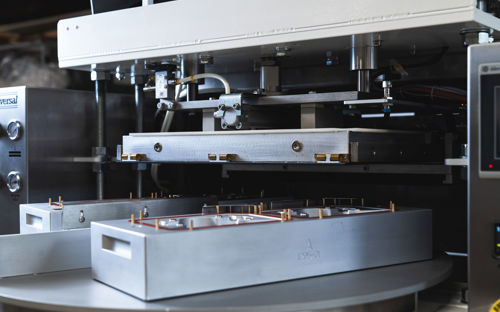
“Chosen by leading medical and pharmaceutical companies worldwide, the Universal machine offers exceptional flexibility for your packaging needs.”
Versatility for every application.
From medical devices to pharmaceutical products, the Universal range adapts to various blister packaging needs in the medical industry. It accommodates a wide range of forming materials, including PVC, PETG, PETGAG, APET, and polystyrene, along with heat-sealable lid materials like cardboard, plastics, aluminum, foil, Tyvek, medical paper, or Mylar.
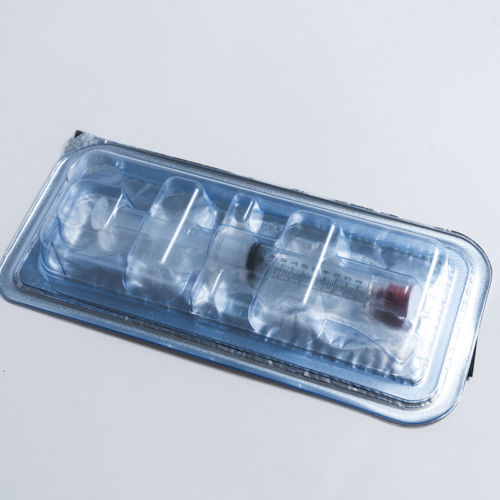
Continuous workflow,
enhanced productivity.
The Universal machine operates on two identical tooling blocks placed on rotary turntables, ensuring a seamless operation flow. With a capacity of over 600 packages per hour across many applications, it optimizes productivity without compromising on quality or precision.
Cost-effective and extremely user-friendly.
The Universal range offers low investment costs, portability, and an easy validation process. Its inexpensive tooling, fast tool changeover in just 4-15 minutes, and no need for preformed blister stocking optimize your workflow and save valuable time, space, and resources. And with its intuitive touch screen interface, operation becomes effortlessly efficient.
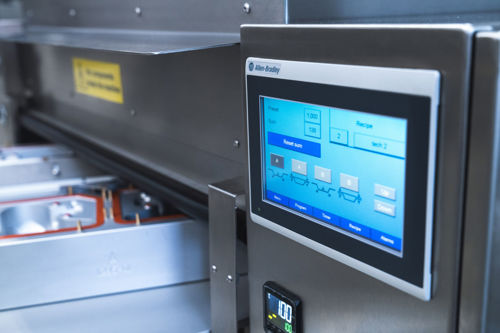
Your advantages
Boosts efficiency:
Forms, fills and seals with one machine
Versatile functionality
Combined forming and sealing
Forming alone
Sealing alone
Cost-effective
Low investment, high returns
Optimized workflow
Intuitive interface, fast tool changes
Trusted solution
Chosen by leading medical companies worldwide
Customization options available
UNIVERSAL MACHINES | 301 S | 301 FS | 301 FSX* | 501 FS | 501 FSX* | 701 FSX* |
---|---|---|---|---|---|---|
Forming & Sealing function: | Sealing only | Yes | Yes | Yes | Yes | Yes |
Turntable: | Automatic | Automatic | Automatic | Automatic | Automatic | Automatic |
Program change: | Automatic | Automatic | Automatic | Automatic | Automatic | Automatic |
Heating plate (mm): | 200 x 400 | 200 x 400 | 200 x 400 | 300 x 500 | 300 x 500 | 300 x 700 |
Max. blister depth (mm): | 100 | 100 | 100 | 100 | 100 | 100 |
Max. sealing pressure at 7 bar (kg): | 2000 | 2000 | 2000 | 2000 | 2000 | 2*2000 |
Heating temp diff. Form & Seal: | No | No | Yes | No | Yes | Yes |
Heating plate output (W): | 1600 | 1600 | 2500 | 2100 | 3500 | 5100 |
Air consumption (liter/cycle at 7 bar operating pressure): | 30 | 30 | 38 | 30 | 38 | 68 |
Max. load (amp): | 10 | 10 | 16 | 10 | 16 | 16 |
Mains connection (V): | 230 + PE | 230 + PE | 3x400 + PE | 230 + PE | 3x400 + PE | 3x400 + PE |
Weight (kg): | 265 | 265 | 310 | 320 | 375 | 480 |
* The FSX models allow for heat differentiation, enabling two different temperatures for forming and sealing, respectively. This ensures better product protection during the sealing process and allows for the use of various sealing materials.